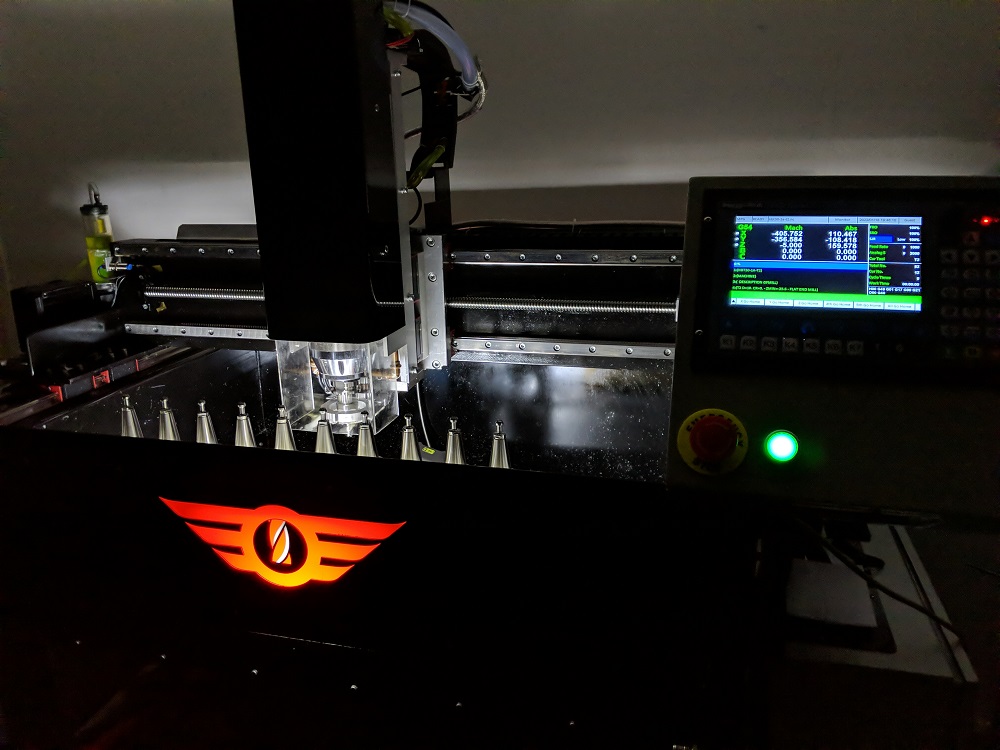
When the mainstream media says the world is going to hell in a handbasket, the best thing to do is turn off the TV and remove all the bookmarks to their websites. Just. Don’t. Look. Interestingly, when I did this, there seemed to be a rather large hole left behind. It’s surprising how much time was sucked away to all that nonsense.
Unfortunately, I’m not the type to be idle. This hole was quickly replaced with a craving to “do something”. I’d had this project in the back of my mind for a while, and always dismissed it as *just a little bit crazy*. Maybe this was the time.
I’d already had some previous history with making machines. Frustrated with not being able to find a Computer Numerical Control (CNC) laser cutter that met my size and power requirement, I made one. That project turned out pretty well, and the laser cutter has been put to use on various little projects. Two dimensional cutting, however, was quite limiting. What I really needed… was a CNC mill!
Any worthwhile project starts with unbounded research, and I drank down all I could find. One particular DIY build caught my eye and the stage was set. I fired up the CAD and modelled up the initial design concepts and then came a stark realisation: I want to make a precision machine without using any precision tools. That, Ladies and Gentlemen… is quite the magic trick. Back to the CAD… Back to the research… Back to the proverbial drawing board.
Iteration is what makes good ideas great, and I have to say, there was quite some of it. The goal was simple: a design that did not rely on any precision machining operation, but rather had adjustments where needed so that the assembly could be tuned along the way. I hit that goal… almost. I had to outsource one operation; grinding the gantry face to be flat.
The build went to plan. Mostly. I made a couple of upgrades soon after getting it operational. These upgrades were done because it became clear that the capabilities of the mill were beyond what I had initially hoped for, and it seemed like a good idea to stretch its legs just a little. I upgraded the X and Y axis motors from closed loop steppers to AC Servos, replaced the well-out-of-support software running on an old netbook with a dedicated CNC controller, and swapped to a larger spindle motor with Automatic Tool Change capability.
A Hammer looking for a Nail
Ok, so the obvious question that should be ringing in your ears is… Why?
I started out on this project to build a machine. I had no real idea about what I would end up making with it once complete. I got the”Why?” from everyone I told about my plans. The answer of “Dunno” to the question of “What are you going to build with it?” was returned with a look that crazy people must see often. I was now a confirmed nutter, apparently. I prefer to think that wise men throughout the ages have observed that once you have a hammer, you see nails everywhere. I was sure that would be the same for me.
Confluence with Bitcoin
In parallel with these shenanigans, I was also deep down the Bitcoin rabbit hole. Long past the “buy it and leave it on an exchange” point, and also past the “don’t you even node, bro?” stage, I had several hardware wallets that I had played with to more or less of a degree.
What was overwhelmingly common to all of them was they all seemed a bit… plastic… fragile… some literally held together with zip ties. I’m all for the bare printed circuit board and wires look, or the “oops, I washed it again look” of a USB flash drive, however this didn’t really match my experience of Bitcoin.
Bitcoin, to me, is akin to either Alien tech or something dropped here by a time-traveller with hindsight already engineered in. Its brilliant combination of previously disparate but individually clever components, capped off with a small amount of additional magic seems other-worldly. I guess others throughout history have had similar experiences in their own time, such is the way of advanced technology.
The system is robust. It is antifragile. It is empowering, inclusive, precise, and seemingly unstoppable. It feels solid. It feels like something I can save my time in. Something I can be sure will not bait and switch that time away when I come to spend it.
And yet these “class leading” best practice security devices for holding that time safe seemed a little…. science project / plastic / machine washable. Fragile. Not very Bitcoin.
So one afternoon I opened the CAD software with a hardware wallet and my callipers at hand and started to design something that might help transform the device into something that better represented Bitcoin’s qualities. This was a totally selfish project; something for me and my device. I had thought that apart from the inevitable cockup (or “prototype” as us engineers like to call them) I’d only be making one. One for me.
As my only customer, I indulged all of my own desires for precision, for quality, for shine. After version seventy-something, it was at a place I was quite happy with. I cut a prototype. I made more tweaks. I iterated. The result was very satisfying, to say the least.
A few twitter posts and some positive feedback from some other plebs and here we are. I have been buying more devices, working on some other designs, and making some more prototypes. Each of which is very satisfying and following the same initial ethos:
“To transform bitcoin hardware devices into objects that reflect the precision, quality and value that Bitcoin truly represents.”